Plastic extrusion for efficient, scalable manufacturing solutions
Plastic extrusion for efficient, scalable manufacturing solutions
Blog Article
A Comprehensive Guide to the Refine and Advantages of Plastic Extrusion
In the large world of production, plastic extrusion emerges as a essential and very efficient process. Altering raw plastic right into continual profiles, it caters to a myriad of industries with its remarkable adaptability.
Recognizing the Basics of Plastic Extrusion
While it might appear complex at first look, the process of plastic extrusion is fundamentally easy. The process starts with the feeding of plastic product, in the type of pellets, powders, or granules, right into a heated barrel. The designed plastic is after that cooled, strengthened, and cut into wanted lengths, completing the process.
The Technical Refine of Plastic Extrusion Explained

Types of Plastic Suitable for Extrusion
The choice of the appropriate sort of plastic is a vital facet of the extrusion procedure. Numerous plastics provide special residential properties, making them more suited to specific applications. Polyethylene, as an example, is commonly used due to its low cost and easy formability. It provides exceptional resistance to chemicals and dampness, making it excellent for products like tubing and containers. Likewise, polypropylene is one more popular option because of its high melting point and resistance to tiredness. For even more durable applications, polystyrene and PVC (polyvinyl chloride) are often chosen for their strength and toughness. Although these are typical options, the choice ultimately relies on the specific needs of the item being produced. So, comprehending these plastic kinds can dramatically boost the extrusion procedure.
Contrasting Plastic Extrusion to Other Plastic Forming Techniques
Comprehending the kinds of plastic appropriate for extrusion paves the method for a wider conversation on exactly how plastic extrusion stacks up versus other plastic forming techniques. Plastic extrusion is unmatched when it comes to developing continuous accounts, such as gaskets, seals, and pipes. It also allows for a consistent cross-section along the size of the product.
Trick Advantages of Plastic Extrusion in Manufacturing
In the world of manufacturing, plastic extrusion supplies many significant benefits. One remarkable benefit is the cost-effectiveness of the procedure, that makes it a financially attractive manufacturing method. Additionally, this technique supplies remarkable item versatility and enhanced production speed, consequently raising overall production performance.
Cost-efficient Production Method
Plastic extrusion leaps to the forefront as a cost-efficient production technique in manufacturing. This process stands out for its capability to produce high volumes of product rapidly and successfully, supplying suppliers with significant financial savings. The key expense benefit is the capacity to use cheaper raw products. Extrusion uses thermoplastic products, which are much less costly compared to steels or ceramics. Additionally, the extrusion procedure itself is relatively simple, decreasing labor costs. Additionally, plastic extrusion calls for less power than standard production methods, contributing to lower operational prices. The process also decreases waste, as any type of excess or malfunctioning materials can be recycled and recycled, giving an additional layer of cost-effectiveness. Overall, the monetary advantages make plastic extrusion an extremely eye-catching choice in the manufacturing market.
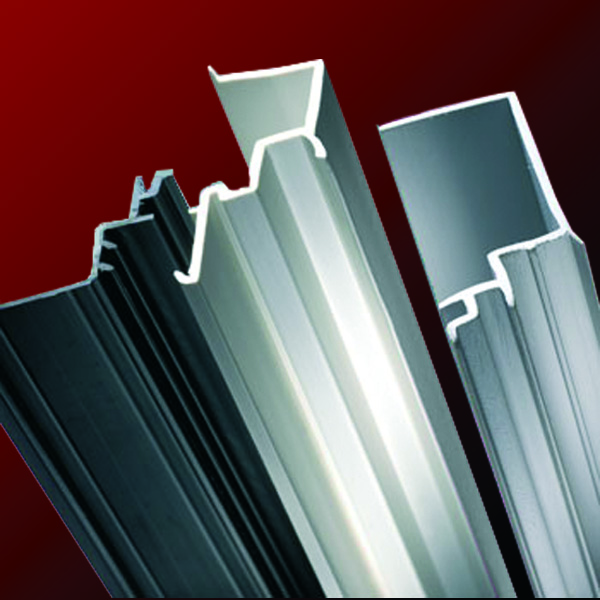
Superior Product Flexibility
Beyond the cost-effectiveness of plastic extrusion, an additional significant advantage in making lies in its superior item flexibility. This makes plastic extrusion an excellent service for sectors that call for tailored plastic see this here components, such as vehicle, construction, and product packaging. In essence, plastic extrusion's product versatility cultivates development while enhancing functional performance.
Boosted Production Speed
A substantial advantage of plastic extrusion hinges on its enhanced manufacturing rate. This production procedure enables high-volume manufacturing in a reasonably brief time period. It is qualified of generating long, continuous plastic accounts, which considerably lowers the manufacturing time. This high-speed manufacturing is particularly beneficial in markets where big amounts of plastic parts are needed within tight deadlines. Couple of various other production procedures can match the rate of plastic extrusion. In addition, the ability to preserve consistent high-speed production without sacrificing product high quality sets plastic extrusion besides various other methods. The boosted production rate, for that reason, not just enables manufacturers to meet high-demand orders but additionally adds to increased performance and cost-effectiveness. This helpful attribute of plastic extrusion has actually made it a favored choice in numerous sectors. our website
Real-world Applications and Effects of Plastic Extrusion
In the realm of manufacturing, the method of plastic extrusion holds extensive significance. The economic advantage of plastic extrusion, mainly its cost-efficient and high-volume outcome, has changed production. The industry is persistently striving for developments in recyclable and eco-friendly products, showing a future where the advantages of plastic extrusion can be maintained without compromising ecological sustainability.
Verdict
Finally, plastic extrusion is a very efficient and effective approach of changing basic materials into diverse items. It uses many advantages over other plastic creating approaches, including cost-effectiveness, high output, marginal waste, and style adaptability. Its effect is exceptionally felt in various sectors such as building and construction, vehicle, and durable goods, making it a pivotal procedure in today's production landscape.
Delving much deeper into the technical procedure of plastic extrusion, it begins with the selection of the suitable plastic product. Once cooled down, the plastic is cut right into the required lengths or wound onto reels if the product is a plastic film or sheet - plastic extrusion. Comparing Plastic Extrusion to Various Other Plastic Forming Techniques
Comprehending the types of plastic suitable for extrusion leads the way for a more comprehensive conversation on how plastic extrusion piles up against various other plastic click here for info creating techniques. Couple of other production procedures can match the rate of plastic extrusion.
Report this page